Welcome to all those who have recently
signed up for our
free email newsletter!
Part
5 - What's All The Talk About Electronics?
What
do I need to know? What do I need to do?
Back in Part 3 we
asked these questions and some insight. In Part 5 we will answer the
first two questions with more specifics.
What do I need to know
about electronics now that computers are involved?
What level of training
do I need in electronics?
By the way, stay
connected to our email newsletter list. We will very soon announce by
email a new web site where vehicle service technicians can access our 60
lesson training program called "The" Vehicle Electronics
Training Program for on-line study.
For now, let's discuss
what technicians should do about vehicle electronics training in today's
vehicle industry. We have seen dramatic changes in electronics in just
the last two decades. One area specifically is construction of PCBs
(printed circuit boards). Electronic components have become more
miniaturized than ever before allowing complex electronic circuits to be
created in smaller packages. This makes circuit boards much smaller and
less expensive to produce, but practically impossible to repair by human
hands. They are simply too small. Although very advanced PCBs are very
difficult to repair, they have created a revolution in electronics
training.
Here are some examples of what I'm talking about. The first
illustration in Figure 1 shows the electronic component size found in
vehicle on-board control units in the late 1980's compared to a 10 cent
dime.
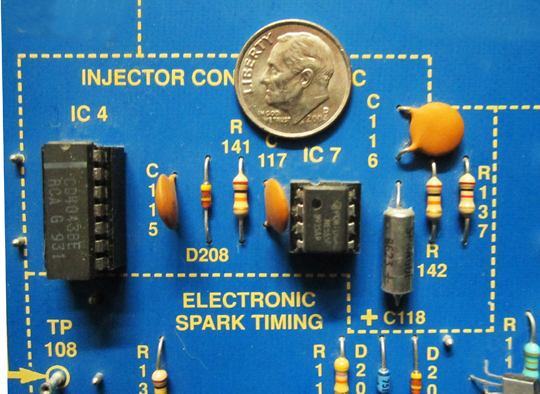
Fig.
1
Electronics
components mounted on an old style PCB
Notice the size of the
fixed carbon resistors, they are the components mounted vertically with
painted color bands indicating their resistance value. The light orange
disc capacitors with two leads lying flat at the top right, the other two
mounted vertically compared to a dime are easy to replace by hand if
needed. There are two integrated circuits large enough to be de-soldered
and a new IC installed, if needed. It is also possible to measure the
voltage or the waveform with the lab scope on any of the pins of an IC
that are physically this large.
The size of these
components are quite easy to handle by human hands and a needle nose
pliers. The components can be inserted into the circuit board and
soldered in place with little trouble and average eyesight. Also consider
how large the size of the circuit board and how heavy it would be
containing a complete circuit consisting of several ICs, power
transistors, multiple resistors and capacitors.
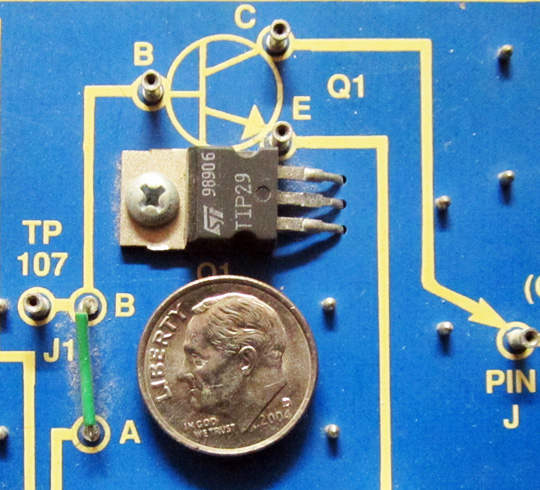
Fig. 2
Power Transistor mounted
on a PCB
The power transistor is almost as large as a dime. An
electronic technician would be trained in electronics school to test the
transistor with the proper type of ohmmeter and look for a bad internal
transistor junction. He would also be trained in an electronic school to
measure the voltages and waveforms on the appropriate transistor leads.
If the transistor is
found to be defective, the three transistor leads can easily be
de-soldered from the circuit board. Remove the mounting screw, de-solder
the three leads, remove the transistor, insert a new transistor, install
the mounting screw, and re-solder the three leads. This would be a simple
task for an electronics technician with a soldering iron and needle nose
pliers. This was common PCB repair in the old days. Printed circuit
board technology has come a long way in the last 25 years.
In Figure 3 below, we
see a photograph of a modern day computer printed circuit board. Notice
the small size compared to the size of a 10 cent dime and the rows of tiny
"chip" resistors and other circuit components.
Fig.
3
Small electronic
component size compared to a 10 cent coin
Measuring voltage and
waveforms at the smaller IC pins is more tedious than before. The probe
tip could easily short two pins together and possibly destroy an IC.It
has reached the point where the circuit boards contain miniature
components that are almost impossible for a human to replace. I can tell
you from personal experience trying to repair these new circuit boards
with "chip" components when they first began to arrive in
vehicles in the late 1980's, was a nerve racking experience. Trying to
replace one of those tiny "chip" components and solder it at
both ends while holding it in place with a needle nose pliers took
patience and skill. It did not take long for manufacturers to realize
these tiny "chip" components could not be replaced by human
hands.
As a result of this
change in electronic component size and PCB construction, the training
required of technicians to repair circuit boards began to decline.
Vehicle manufacturers decided to replace defective control units with new
ones rather than have them repaired by electronics technicians. Today,
most onboard computers, due to this new PCB technology, are replaced
rather than repaired. This also affects other segments of the electronics
industry. One example, if your home/office PC develops a problem on the
motherboard, it is more economical to buy a new motherboard rather than
attempt to repair the old motherboard.
Therefore, schools
that taught electronics for circuit board repair down to the component
level began closing down due to low student enrollment. There is a
declining need for electronic technicians with skills to repair circuit
boards in today's technology. As a result, many of the electrical and
electronic troubleshooting skills that were taught in electronic schools
in the past is being lost. They are not being passed on to the next
generation. Some of these skills would be helpful for a vehicle service technician
to test a vehicle electronic system.
For example, the
technique of testing a transistor with an ohmmeter is being lost. Of
course, a service technician today would never be expected to test and
replace a transistor in an onboard computer. But knowing how to test
solid-state components like transistors and diodes with an ohmmeter can
be adapted in other areas of vehicle maintenance. This skill could be
used to test L.E.D. lamp assemblies and some sensors containing
solid-state components. I could cite several examples but due to the
length of this article I only want to address one.
A few months ago I was
conducting an electrical - electronics training class in a fleet
maintenance shop. The technicians in the class mentioned they were having
trouble with an emergency flashing light unit mounted on many of their
vehicles. Some vehicles would have two or four of these units mounted on
the vehicle. They would last about six months then they would have to be
replaced at almost $200 a pop. We disassembled one of the defective units
and on the circuit board was a power transistor. I tested it with my
ohmmeter and saw that it was bad. It would have been a simple task to
de-solder the defective power transistor and install a new one to repair
the unit. The cost to repair by replacing the power transistor would have
been less than $20 and taken 10-15 minutes.
Let me say this loud
and clear. I do not recommend, nor do I imply a vehicle service
technician ever open up an on-board computer and attempt to repair the
circuit board. These emergency light assemblies with solid-state
components are a different matter and perfectly safe to look inside and
repair. But NEVER do that with an on-board vehicle computer.
Today it is more
economical to replace an on-board control unit rather than train and pay
an electronics technician, provide an expensive electronic repair
workstation to repair the original circuit board when it develops a
problem. It is cheaper in most cases to build new on-board control units
rather than repair old ones. So many manufacturers ask why continue to
train electronic technicians to repair computer circuit boards down to
the component level when a brand-new unit can be manufactured at less
expense?
I think we can all
agree with that decision, but let's not overlook the need for the proper
electrical - electronics training to help a service technician make the
decision that the problem is inside the computer or something in the
vehicle circuit has caused the computer failure. Let's eliminate the
guessing game that the on-board computer is bad or the problem is in the
vehicle circuit.
What do I need to know
about electronics now that vehicle computers are involved?
Today's vehicle
electronic technician does not have to study in depth electronics theory
to be able to repair computer circuit boards. For example an electronics
technician is taught to calculate the inductive reactance in ohms of a
coil in a circuit at a specific frequency. He is taught to calculate the
capacitive reactance of a capacitor in ohms in a circuit at a specific
frequency. Neither exercise would be of benefit to a vehicle service
technician. So we can dispense with this in-depth level of electronic
training for a vehicle service technician. What is really needed is a training
program that specifically addresses the skills to handle the electronics
level of diagnosis and repair the vehicle service technician faces with
today's vehicle technology.
What level of training
do I need in electronics?
A vehicle service
technician does not have to become an electronics technician but should
have a clear understanding of the principles of series and parallel
circuits. How circuits work, how circuits fail and how to electrically
troubleshoot any circuit on any vehicle should be the main focus of
hands-on training. A vehicle service technician should understand the DMM
and Current Clamp, not just in theory, but in practical application from
effective hands-on troubleshooting training exercises.
He should understand
technical subjects such as the workings of a coil in a DC circuit and
what parameters he should be concerned with if the coil is controlled by
an expensive on-board computer, such as spike voltage protection. He
should understand the importance of capacitors in DC circuits. This would
be beneficial to vehicle service technicians dealing with hybrid vehicles
employing "ultra-capacitors."
This is the ultimate
goal of electrical electronics troubleshooting training for vehicle
service technicians. The training should encompass hands-on
troubleshooting techniques that allow a technician to perform circuit
tests to reveal circuit problems even when service information is not
available and the technician has little or no previous knowledge of the
circuit. This may sound like a tall order but this level of
electrical-electronics troubleshooting training is available right now.
Visit our web site for
all the details about our electrical-electronics training programs that
address these issues and more. These three links will help you navigate
our main website.
If you are a service
technician click here.
If you are a shop owner
click here.
If you are a teacher click here.
These links will
explain our various training programs and give you direction on how to
proceed.
If you are interested
in the 60 lessons and would like more information about
"The" Vehicle Electronics
Training Program click here.
Stay connected to our email newsletter list. We will very
soon announce by email a new web site where vehicle service technicians
can access our 60 lesson training program called "The" Vehicle Electronics
Training Program for on-line study.
Technicians will study
the lessons online and print out their own lessons if they wish. We will
be offering a lifetime membership to this website. We also are planning
some exciting additions to the 60 lesson home study course that will also
be provided over time. We will let you know as soon as this website is
posted on the Internet and ready for enrollment.
The next installment,
Part 6, we will answer some of the following questions.
How do I test a driver
transistor circuit?
What is required
testing a vehicle computer?
If the circuit doesn't
work, how do I tell what is the reason for the failure?
Is the problem in the
computer or a problem in the vehicle circuit?
Can a computer circuit
fail because there is a problem in the vehicle that will cause the new
computer to fail after I replace it?
What do I need to do
to increase my electronics knowledge without over kill?
How much electronics training is enough?
Look
for our special announcement.
Vince Fischelli
Director of Training
Veejer Enterprises
Web site: www.veejer.com
Email: vince@veejer.com
Phone: 972.276.9642
Fax: 972.276.8122
|